REFERENCES
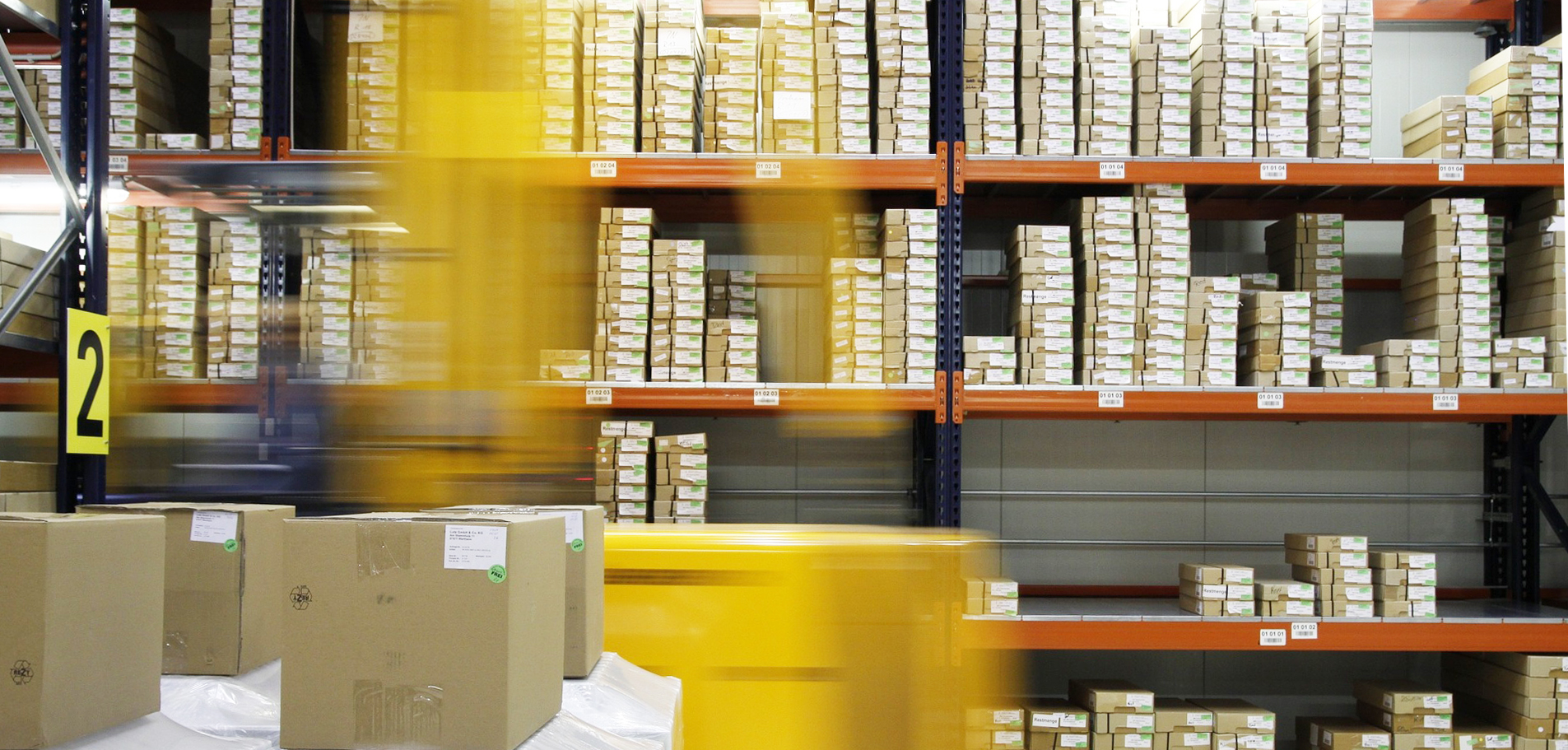
Vaillant Group
TechnoCargo Logistik and the Vaillant Group Standardize Calculations for Quotations
12.06.2018
Permanent Price Comparison along the Supply Chain
The standardization of price calculations has been the focus of a project at TechnoCargo Logistik, the logistics service provider for the Vaillant Group. The goal of both corporations was to design the warehouse price list at TechnoCargo in such a way that it reflects the work required for the personnel and the equipment used in the processes and ultimately creates transparency for all the warehouse activities. The new logics in the price calculation system is based on the process analysis provided by MTM.
It was a logical step for TechnoCargo Logistik to draw up a new price calculation system. The previous cost structure had been determined jointly with employees of the Vaillant Group using the open-book method. However, the prices did not reflect the specific work required by personnel or the equipment used in the individual areas. “This meant that it wasn’t possible to explicitly designate the prices per unit either. “We had to change this situation,” said Thomas Marquardt, the authorized signatory at TechnoCargo Logistik Beteiligungsgesellschaft mbH. Switching to process-based calculations on the basis of MTM finally met the goal of providing complete process and price transparency.
Process and work-based price calculations with MTM
The process and work-based price calculations were introduced at TechnoCargo Logistik with support from Ann Schmitz, a project engineer at Deutsche MTM-Gesellschaft mbH, and Matthias Kraneis, the MTM coordinator from the industrial manufacturing department at the Vaillant Group. The processes, ranging from the incoming goods for the different heating, ventilation and air-conditioning units and accessories or spare parts to outgoing goods and even the production of spare parts and controlling, were analyzed and documented using MTM. This involves, for example, providing supplies of materials, handling the goods, packaging, picking and a great deal of the administrative department’s work. “MTM enables us to now prove to the customer why it has to pay a certain amount for a package or pallet precisely in line with the process”, says Ann Schmitz, describing the system. Matthias Kraneis adds, “it’s also been possible to design and handle the processes for Vaillant more cost-effectively – and TechnoCargo Logistik can therefore operate at lower costs too. This means a permanent price comparison along the supply chain!”
The process and work-based price calculations provide benefits both for the supplier and the customer.
The benefits for TechnoCargo Logistik (supplier):
- Maximum transparency leads to an improved understanding of the process and comprehensively identifying any savings potential.
- The expertise regarding the process design and assessment of the work can be transferred to other departments in the corporation (e.g. administrative processes).
- A precise knowledge of methods leads to clear, competitive quotations.
- The standard model for calculating the process and work costs introduces a new quality level for capacity planning and cost forecasts.
The benefits for the Vaillant Group (customer):
- International standards enable benchmarking at an operational level between the supplier and the customer.
- The standard process documentation can be used as a detailed description of the requirements for logistics tenders and help the service partner to calculate its quotation as competitively as possible.
- The process-based price list forms the basis for rolling it out to other Vaillant warehouses.
- Price list negotiations can be directly applied to the process triggering the costs and enable clear statements about their development.
“Detailed calculations, which create complete transparency, only function well by using process-based price lists”, says Matthias Kraneis, with great certainty. “The new price list logics enable the assignment of each price list item to the individual activity level. Thomas Marquardt emphasizes the role played by MTM at this point. “I can only exactly calculate the costs and benefits of any optimization measures on this basis – that is to say, when a new forklift with the latest technology or a lifting aid pays off, for example.”
Complete transparency throughout all the departments
All in all, the project has created complete transparency in all the departments that have been considered – and has led to 18 concepts to introduce potential for improvements. According to Matthias Kraneis, they include, for example, the change from the supplier’s item number to a defined Vaillant item number, which reduces the administrative work by 148 hours every year. The managers at TechnoCargo Logistik can make use of further potential in the planning work on this basis. The server-based MTM software solution known as TiCon, which is used by the Vaillant Group, also provides support for this. Two industrial engineers at TechnoCargo Logistik have now completely taken over the management of the data.
In order to identify interfaces between the customer and the service provider along the supply chain in the future too and make use of synergy effects, the MTM Practitioners, who have been trained internally at TechnoCargo Logistik, have been included within the Vaillant Group’s industrial team of MTM experts. The plan is to extend the MTM activities to TechnoCargo Logistik’s activities in the UK and Slovakia too.
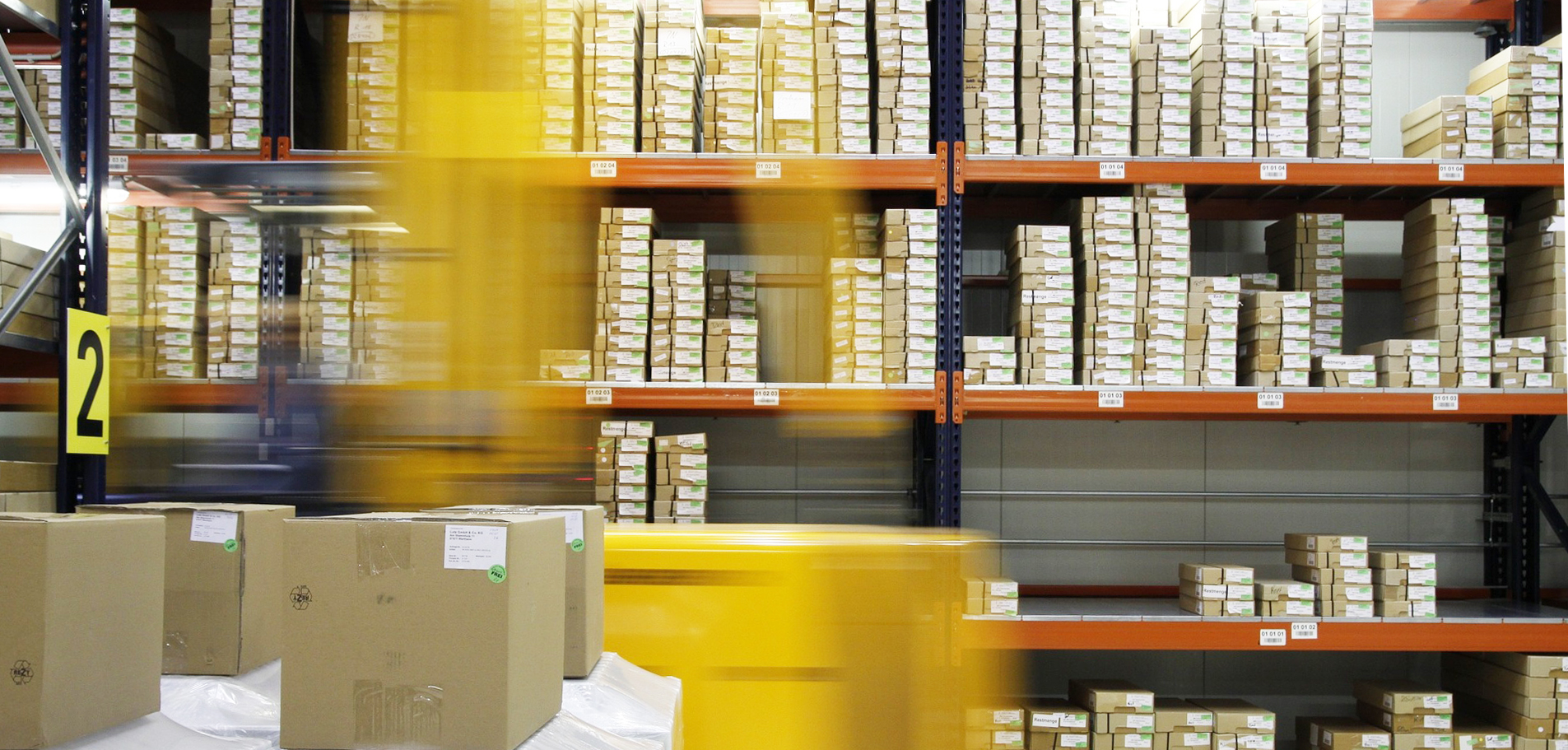
Vaillant Group
MTM as International Standard at Vaillant Group
20.06.2016
Sustainable success with a worldwide training concept
The Vaillant Group with its headquarters in Remscheid/Germany has been one of the world's leading suppliers of innovative heating technology for more than 140 years. More than 12,000 employees at 13 production and development sites in Europe and China work on energy-saving technologies and products for heating, cooling and hot water production. In 2012, management and central Industrial Engineering started a project for sustainable productivity increase with the help of the MTM process. The aim of the project, which comprises a total of five stages, was to build up company-specific competencies for MTM application within the global group of companies. The worldwide rollout was completed at the beginning of this year. Now each of the ten Vaillant production sites has an MTM structure and suitably trained industrial engineers on site.
Not short-term successes in one plant or another, but sustainable productivity increases in the entire Group is the aim of Vaillant's Management Board – and the task of the Group's Industrial Engineering (IE). The path to the goal leads via complete transparency in workflows and processes, ergonomically designed workplaces, the introduction of a standard performance, the establishment of IE competence in all production plants, a standardised procedure – and thus via MTM. The planners should no longer have to rely on times or experience values measured with a stopwatch, as in the past, but should have an exact, comprehensible database at their disposal. It was also important to the central IE that MTM is a process that considers the entire value-added chain - from product development and design to production, service and logistics.
The prerequisite for the successful rollout of MTM was the establishment of a corresponding structure with internal MTM competence as well as the development of a common understanding of MTM among employees, managers and works councils. Two so-called MTM experts were trained per plant to promote the topic of MTM and to support the MTM operators entrusted with the daily business with their know-how. Each MTM operator in turn has completed training as an MTM practitioner and is thus fit in MTM-UAS, the process module system on which the company-specific database at Vaillant is based. The MTM structure in the Vaillant Group is completed by an MTM engineer. Matthias Kraneis from the Group-IE coordinates the worldwide MTM application at Vaillant, has here an interface function with the Works Council of the Vaillant Group and also maintains contact with the MTM consulting company, which further supports the company if required.
The area-wide introduction of MTM took place over a period of three years. In 2012 and 2013 there was a first performance project at the Trencin plant. The first training courses for MTM practitioners started in 2014 at the Belper plant in Great Britain. In addition, the first company agreement for the training of MTM experts was concluded here. 2015 the MTM software TiCon was implemented. An international team of IT & IE experts developed the Vaillant database, which the MTM experts can access worldwide. This was followed by further pilot projects at each location and finally the global rollout at the end of 2015/beginning of 2016.
Project Manager Matthias Kraneis considered it particularly important to involve the employees, team leaders, production managers and works councils in each plant from the very beginning. "Among other things, we picked up the people with day workshops and business games so that they could experience for themselves what MTM means". It has also been shown that transparency and ergonomic work design are two important levers for developing a common understanding of the following measures.
The fact that the introduction of MTM has been worthwhile can be seen by all those involved: By applying the standard industrial engineering procedure, productivity increases of up to 15 percent have been achieved. A company agreement on the global MTM application makes the work of the planners in the group of companies much easier. The employees are motivated in their work. For the near future, an expansion of the MTM core team and the know-how in the direction of production-oriented design (ProKon), ergonomics and logistics is planned. Already in 2018, there will be four MTM experts at each production site, who are also trained in the application of the ergonomics assessment tool EAWS (Ergonomic Assessment Worksheet) and MTM logistics.