REFERENCES
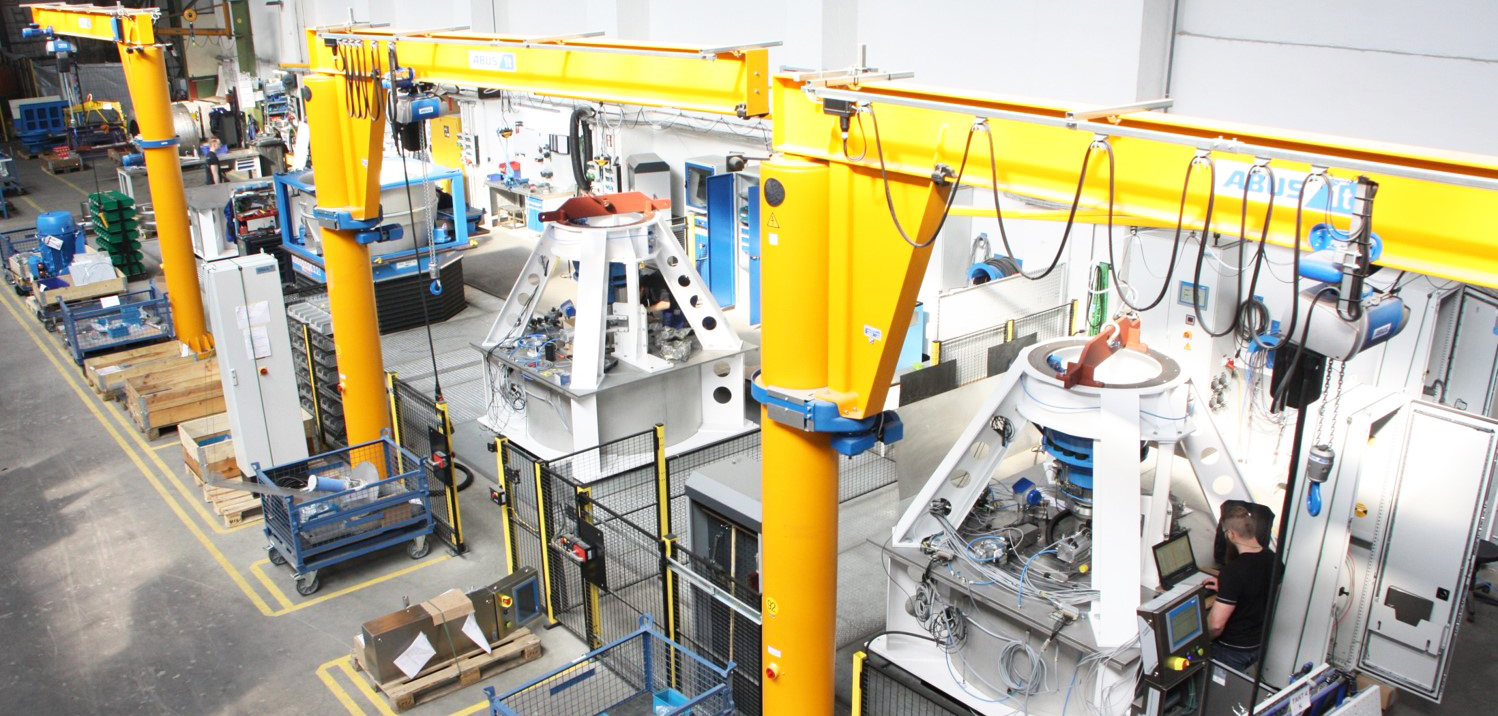
BMA BRAUNSCHWEIGISCHE MASCHINENBAUANSTALT AG
Productivity Up – Inventories Down!
28.10.2019
Engineering Corporation Increases Efficiency in Production Using MTM-Based Time Management
BMA Braunschweigische Maschinenbauanstalt has been successfully operating in the market for more than 160 years making centrifuges and pumps for industrial sugar production and refining. The production processes were still similar to those of a manually operated factory even just a few years ago. However, competitive pressure, rising numbers of orders, constantly changing market conditions and customer requirements made it necessary to switch the centrifuge production from a station assembly system to balanced single line manufacturing with a two-shift system; the corporation was therefore able to significantly increase productivity levels. The reason for 60% greater efficiency in production, the increase in production volume to 300 centrifuges and 50 pumps per annum as well as precise product and human resources calculations was the introduction of an MTM-based time management system. The Deutsche MTM-Gesellschaft mbH supported the project as a partner.
“We’re a classic manufacturer of individual items. The product line may be a kind of building block system, but in the end every machine is absolutely unique,” says Dr. Christian Beer, COO and a Board Member at BMA Braunschweigische Maschinenbauanstalt. In order to meet the most important requirements regarding competitiveness – delivery capability, productivity and quality – the corporation faced the issue of finding models to industrialize the production processes three or four years ago. “In my opinion, we needed a pull system: Assembling machines in a defined line balance sequence and delivering them directly to customers”, Beer comments.
„Lean and MTM go very well together“
He believed that a mix of methods between lean and MTM would be most suitable after looking at the Toyota production system and having gained many years of experience with MTM aimed at optimizing assembly procedures geared towards increasing value. “Lean and MTM go very well together. We’ll automate systems where it makes sense. In addition, our corporate philosophy also entails using new technologies and manufacturing according to customer ordering cycles”, says the manager and initiator of the project, describing operations.
Transparency is the key
The first and most important step in establishing a single line production facility was transparency in the process landscape regarding preliminary and main assembly operations. “By using MTM, we were able to determine which content needed to be handled at which work station and when,” Beer adds. During the analysis, problems in the preliminary assembly work also came to light – e.g. during the preparatory work or when making materials available.
“These problems were there all the time, but we simply didn’t see them”, says Beer. “They only became visible through putting on MTM glasses and having structured processes.” The new assembly line was then planned with TARGET times. The goal was to have about 7 h of work content at each work station along the line. The cycle time is a shift so that one machine is completed every shift.
„That wouldn’t have been possible under the old system“
Beer is more than delighted by the results of using MTM. “Firstly, we actually know now about the time values related to the assembly work and, secondly, we’ve become more productive,” the manager emphasizes and adds, “We can now work on our ability to meet delivery deadlines and quality. By having this kind of well-structured process, the corporation is also able to make use of a second shift and increase production. That wouldn’t have been possible under the old system”, Beer comments.
The next steps are clear. The enterprise is aiming to extend the use of MTM to other production areas and particularly help with the switch to robot-supported welding component production. “We have very many setup processes and we want to only produce what is actually sold – and handle the times with MTM,” the manager adds. In general, BMA is moving away from batch production unrelated to customers towards production in line with customer orders. “Productivity up – inventories down – that works now.”
Quicker upward mobility with efficient work organization
Beer himself describes the whole process as a beacon project. “I wanted to show the critics of MTM that assessing manual activities and a significant increase in productivity are possible in engineering too – not just when manufacturing vehicles. This beacon project has also impressed the works council. I went down to the shop floor and showed the employees that things will improve much faster by having good work organization and efficient processes – and nobody can argue with that.”
Bildnachweis:
© BMA Braunschweigische Maschinenbauanstalt AG