REFERENCES
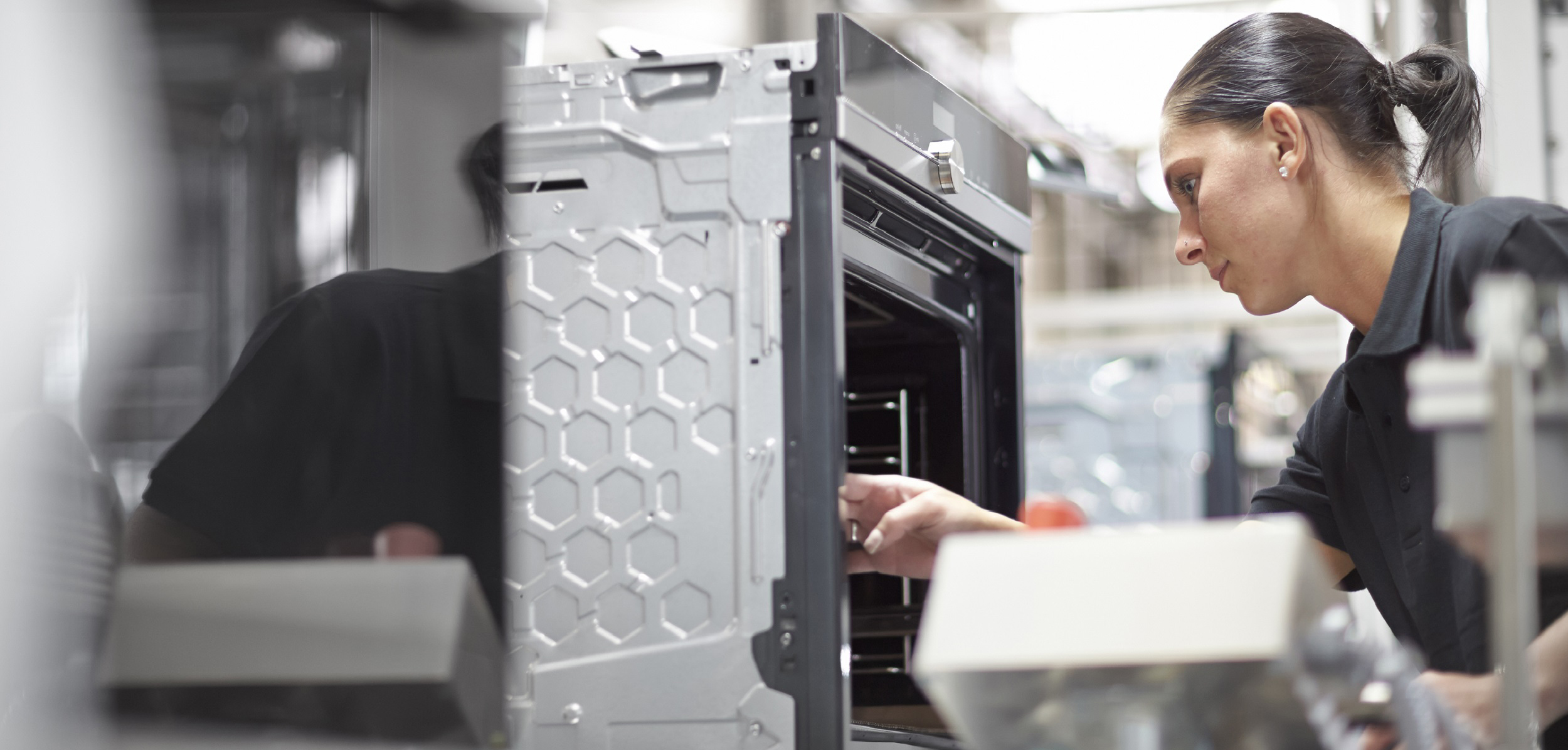
BSH Hausgeräte GmbH
Facts and Figures instead of a Gut Feeling
10.10.2017
BSH Hausgeräte GmbH manufactures stoves and ceramic hobs at its business site in Traunreut. One element in the quality assurance procedure involves visual inspections of the ovens in the stoves to discover any flaws in the enamel finish. This takes place at just one inspection point during all three shifts. The corporation needed to reduce the current cycle time of 13.5 seconds to no more than 12 seconds and therefore increase the number of items per hour. The goal was also to continue managing with just one checking point – i. e. one employee per shift. Klaus Einsiedler, Head of Enameling Surface Technology, provided the objective evidence that this is feasible by using the MTM process building block system for visual inspections. The analysis tool is ideally suited to assess inspection activities that depend on human assessment and decision skills.
„I wanted some objective evidence“
The demands placed on the inspection point are high. The employee has to examine a different stove every 13.5 seconds and has just seven seconds to complete the actual checking procedure. During this time, he or she needs to closely assess a particular number of potential flaw areas and make a decision: Is the unit OK, should it be rejected or is additional work required? If the latter is the case, the errors still need to be categorized and documented. The employee and even Klaus Einsiedler assumed that the planned cycle time of twelve seconds was feasible. But the section manager said, „an assumption is not enough for me to form the basis for extra work. I wanted some objective evidence”. As there are no experts on the subject of visual inspections at BSH Hausgeräte GmbH in Traunreut, the company decided to seek help from outside – and discovered that Deutsche MTM-Gesellschaft mbH could provide assistance.
Planned cycle time backed up by an analysis
The project involved clarifying how much work was involved in the inspection process – i. e. the time required for an employee to check a particular area with a particular size – the so-called inspection area – according to particular criteria. The result was that the planned cycle time of twelve seconds, including the feed-in and removal procedures, is enough! It also meets the goal of managing with just one inspection point. „However, what we’ll do is relieve the employee by means of a colleague working in the vicinity every 20 minutes”, says the section manager. „The employee who isn’t standing at the inspection point can use some recovery time or time for personal needs or look after the reworking of faulty parts. This solution also provides greater variety for what is the exhausting work of visually inspecting units. A second checking point is due to be introduced to enable the company to remain flexible if the number of items rises significantly or if volumes in orders increase at short notice. „However, we’ll generally only use one”, says Einsiedler.
MTM application: design information inclusive
The verification of the planned cycle time was not the only result of the project. The MTM application also provides additional benefits.
The MTM visual inspection analysis tool
- makes the inspection procedures more transparent, plannable and reproducible,
- includes issues related to the design of the inspection or testing point (posture, field of vision, lighting)
- provides help with resolving work organization issues like the duration and frequency of inspection jobs, reducing tiredness or relaxing the eye muscles,
- offers support for selecting tools and encourages targeted working instructions.
„We’ve particularly improved the ergonomics at the inspection point, we’ve optimized the lighting and attached noise or visual protection to reduce the effects from the surrounding area that could impair the inspection procedure”, says Einsiedler, describing the improvements. However, he believes the greatest benefit of the project is that it was possible to guarantee the assumed result with facts and figures – „this has ensured that the works managers and the works council are all on board too.”
Bildnachweis:
© BSH Hausgeräte GmbH
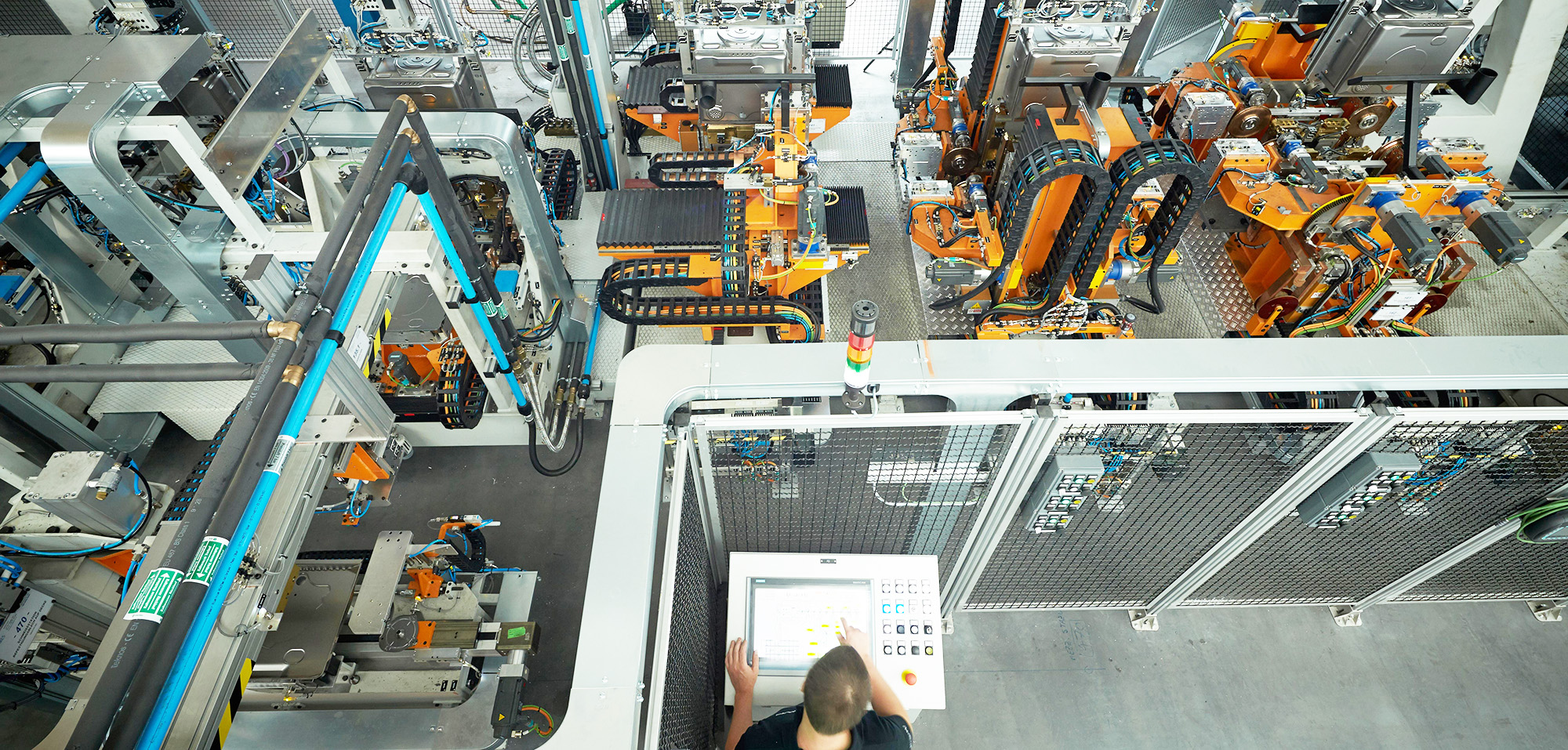
BSH Hausgeräte GmbH
BSH Hausgeräte Uses TiCon für Teamcenter for Integrated Process Planning
13.09.2018
Best Practice: MTM Software Solutions
TiCon für Teamcenter is one of the most important current development topics at the MTM Software Center. The IT solution, which has been developed in close cooperation with Siemens, enables the MTM application to be directly employed in the Easy Plan user frontend of the Teamcenter PLM software produced by Siemens. TiCon für Teamcenter is the major focus of a pilot project for integrated digital process planning at the digital factory at BSH Hausgeräte GmbH. Ralf Digel, Global Information Technology, Digital Factory BSH Hausgeräte GmbH, reported on the corporation’s practical experience with the new MTM software solution as part of this year’s TiCon Users’ Meeting. “BSH,” he said, “has taken great strides in meeting its goal by integrating the TiCon time management software in the Siemens Teamcenter environment – namely to genuinely integrate all the data related to production in a PLM database. TiCon für Teamcenter is currently available for the MTM-UAS, MTM-SD and MTM-MEK process building block systems.
Teamcenter, the Siemens software solution for Product Lifecycle Management (PLM), has been in use around the globe at all the factories operated by BSH Hausgeräte GmbH since 2007/2008. “The current state mainly involves using Teamcenter to manage product-related data in a structured manner and support development processes,” Ralf Digel explained. “The topic of PLM, however, is continuing to develop in a very dynamic way. Two of the greatest challenges involve configuring or planning different options and having a simpler and quicker process for preparing lists of parts. Dynamic change management, in turn, makes it necessary to fully use all the Teamcenter functions,” Digel added. “We have to view the complete version history of a list of parts, for example, keep track of changes within a change number and then be able to provide the parts list that is valid for a certain time.”
One system for all the processes
The Tecnomatix software is available in the current systems landscape at BSH for process planning, line balancing and managing different options. The data that is processed there comes from the TiCon time studies, from EAWS (Ergonomic Assessment Worksheet), which is being extensively introduced in Germany and increasingly used at the foreign business sites too, as well as from the product analysis using the MTM-based ProKon tool (production-oriented design). „By using Teamcenter, we finally want to have a system where all these processes don’t require interfaces and are integrated without any duplication of work,” Digel stresses.
The general goal at BSH has been to optimize the planning workflow in Easy Plan, the user frontend of the Teamcenter software. The direct integration of the web client TiCon für Teamcenter in Easy Plan has several benefits, in Digel’s view:
- Regardless of the department where users are based at BSH, th“ey can log into TiCon directly. There is no need for any change in the user interface.
- TiCon für Teamcenter enables the web application TiCon to be used, regardless of the platform involved. Planners therefore do not need any experience with Teamcenter if they wish to prepare MTM time building blocks. “This enables us to guarantee maximum flexibility when preparing standard times,” says Digel.
- The MTM process building block systems, MTM-UAS and MTM-SBW, which are used at the company, are supported.
- TiCon für Teamcenter makes it possible to manage and use workflow indicators in the value-added process.
- TiCon für Teamcenter can be integrated from Siemens Easy Plan 2.4 upwards.
- The add-on supports several languages for the application (German/English as the standard options; other languages are possible).
The next steps for further developing Easy Plan and TiCon für Teamcenter at BSH Hausgeräte have already been planned. The aim is to replace TiCon3 by TiCon in Easy Plan by 2020 and Tecnomatix as the line balancing tool by 2021 too. Alongside this, the EAWS ergonomic assessment tool is being integrated in Easy Plan.
Picture Copyright:
© BSH Hausgeräte GmbH
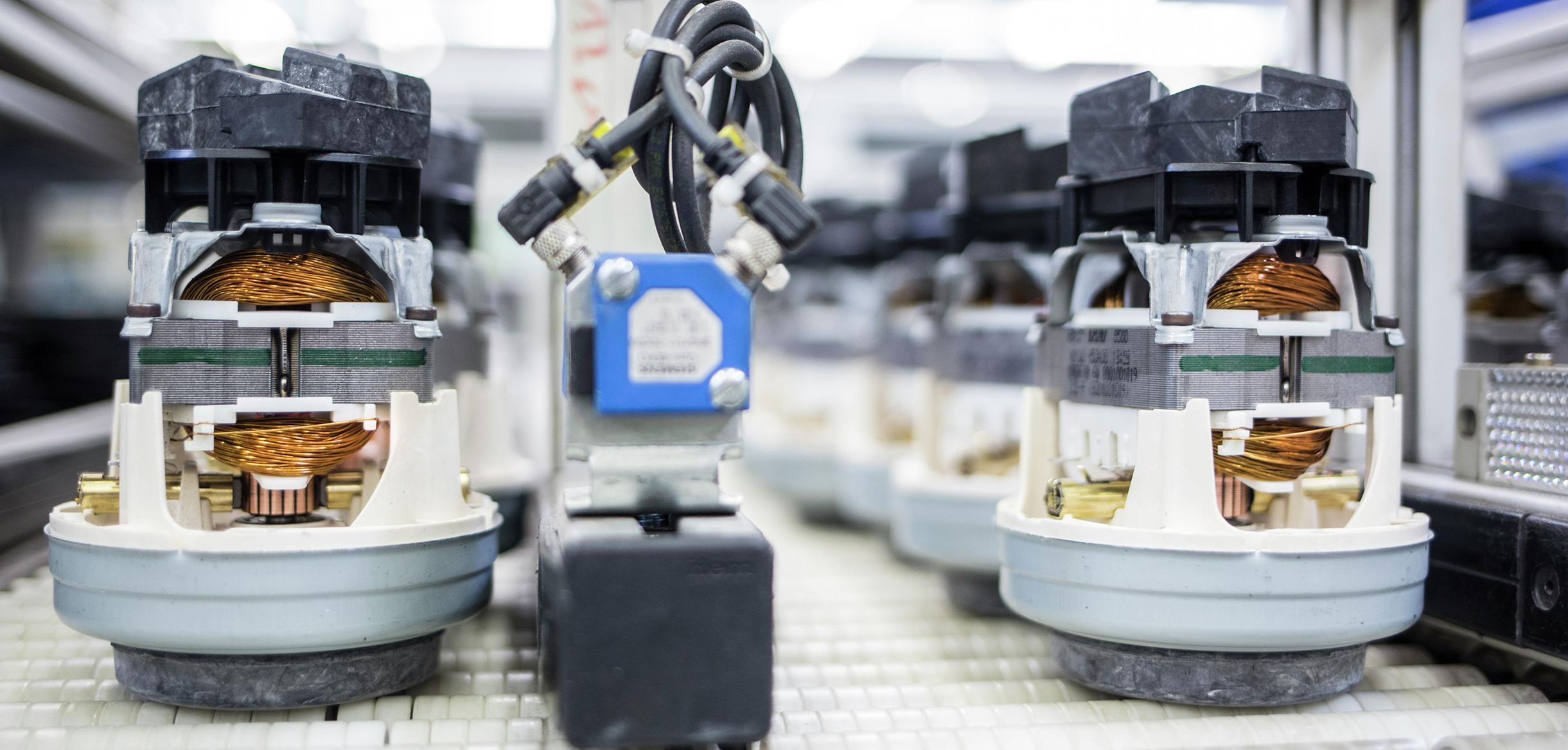
BSH Hausgeräte GmbH
BSH Hausgeräte GmbH optimizes assembly with the MTM process ProKon
14.06.2017
The reduction of assembly difficulties and costs in the vacuum cleaner assembly was the focus of a workshop at BSH Hausgeräte GmbH in Bad Neustadt. The participants learned the advantages of the MTM process ProKon and the positive effects of production-oriented construction also with regard to ergonomic design know the stresses and strains.
When minimizing assembly times, the optimization of the construction-related installation effort is a significant factor. With ProKon processes (production-friendly design) can already be used in the product development phase possible later assembly difficulties, their effects on assembly work and ergonomic stress as well as the cost-relevant factors are identified. The BSH Hausgeräte GmbH makes use of these advantages and does not consider in terms of optimization only the assembly workstations themselves, but also the construction and ist interfaces to production. At the workshop moderated by MTM for reduction of assembly difficulties and costs in the area of vacuum cleaner assembly was therefore carried out by production planners and master craftsmen, responsible for ergonomics and controlling and representatives of the product developers and designers also participate in the works council.
Savings potential of up to 18 percent realized
The participants first acquired a basic understanding of the application of ProKon in the manual assembly, then identified by the example of various vacuum cleaner models the assembly difficulties, ProKon analyses and evaluated design variants with regard to their ease of assembly. This illustrated the effects of difficulties in the assembly process on later assembly times and ergonomic stresses at work stations – and at which point in the product creation process the necessary measures need to be adopted: i. e. at the earliest possible time – as early as the product development or design phase. In the example cases within the scope of the workshop alone through optimization in the design of components a savings potential of up to 18 percent can be realized.
Sustainability instead of short-term effects
But not only in the cost saving or the estimation of the ergonomic risks, the use of ProKon has a positive effect. The procedure requires and also promotes interdisciplinary cooperation within the company. Because with designers, production planners and master craftsmen are the originators of constructive design of components, the persons concerned in dealing with assembly difficulties and the persons responsible for personnel scheduling where there are physical requirements at the workplace. With BSH Hausgeräte is committed to sustainability in such a prospective approach instead of short-term effects, stresses André Piel, Head of Production at BSH in Bad Neustadt. In the meantime, employees have been trained in MTM and further employees trained in the use of EAWS – for André Piel a logical consequence of the application of MTM as a holistic method in productivity management.
Picture Copyright:
© BSH Hausgeräte GmbH