REFERENCES
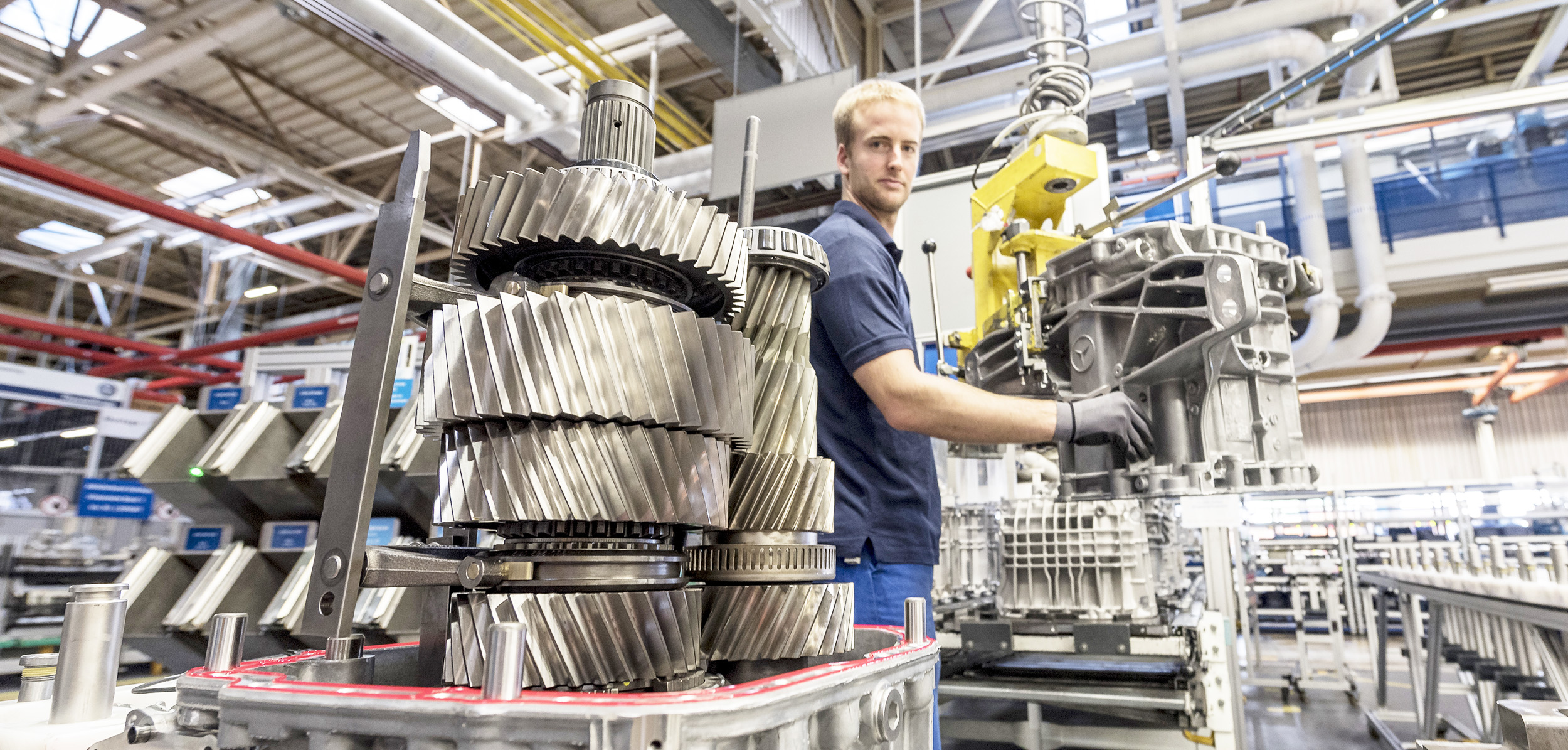
Daimler AG
Mercedes Benz uses MTM to manage the ideal operating situation on the shop floor
14.02.2017
The high degree of variation in the assembly of gearboxes at the Mercedes-Benz plant at Gaggenau places high demands on planning and managing human resources. How many employees with which skills and capabilities are necessary for each shift and how can these employees be used in a flexible manner? A joint project conducted by Daimler AG and Deutsche MTM-Gesellschaft mbH provided the answer to these questions. It focused on productivity improvements using a tool to determine and control the optimum operating situation. This tool is now being used as a new device on the shop floor on a daily basis.
The ideal operating situation describes the optimum utilization of an employee with work content in the work process – while also keeping an eye on the achievable performance level in comparison with the cycle time in order to prevent any waiting times.
The assembly activities on line 2 at the Gaggenau factory were initially analyzed with the Daimler C values at the end of 2015 and the beginning of 2016 – at each assembly point and with each gearbox variant. The C values were checked at this time and adapted, if necessary. The data obtained in the mix of planning and performance analyses not only forms the well-founded basis for planning the use of human resources precisely. The uniform standard for determining times enables a comparison of working methods and ensures the necessary transparency.
During the next stage, an interface for automatically inputting the data for controlling the operating situation was developed for TiCon. The line balancing models for seven different employee scenarios were then logged in the new tool using flow charts. Disruption workshops were held at the bottlenecks. After work methods had been selected, the employees in the groups were able to test the most suitable method. The results or the necessary changes to procedures were then integrated in the operating situation tool. Validation of the operating situation logging tool takes place by daily measuring KPIs (gearbox output according to the tool compared to the loss of gearboxes due to disruption).
A reference month was selected to determine the increase in productivity – and the number of gearboxes assembled and the presence of the employees were observed. These figures were then verified with the new operating situation logging tool. The correct use of employees per working area alone provided an increase of 3%.
Thanks to the all-round approach of MTM advice and the building block logics, i.e. the enhancement options for each building block, Mercedes-Benz is now very satisfied. This also applies to the use of TiCon. The MTM software solution plays an important role in coping with the upcoming tasks. Due to the automatic data integration, it is possible to minimize the manual work, for instance.
The activities on gearbox assembly line 1 at the Mercedes-Benz factory in Gaggenau are being analyzed at the moment. As with line 2, the works council is involved – in addition to representatives from the group, production engineers and colleagues from industrial engineering. The operating situation tool should be available for line 1 too by the middle/end of February 2017. The next step will involve extending the prediction possibilities.
Picture Copyright:
© Daimler AG
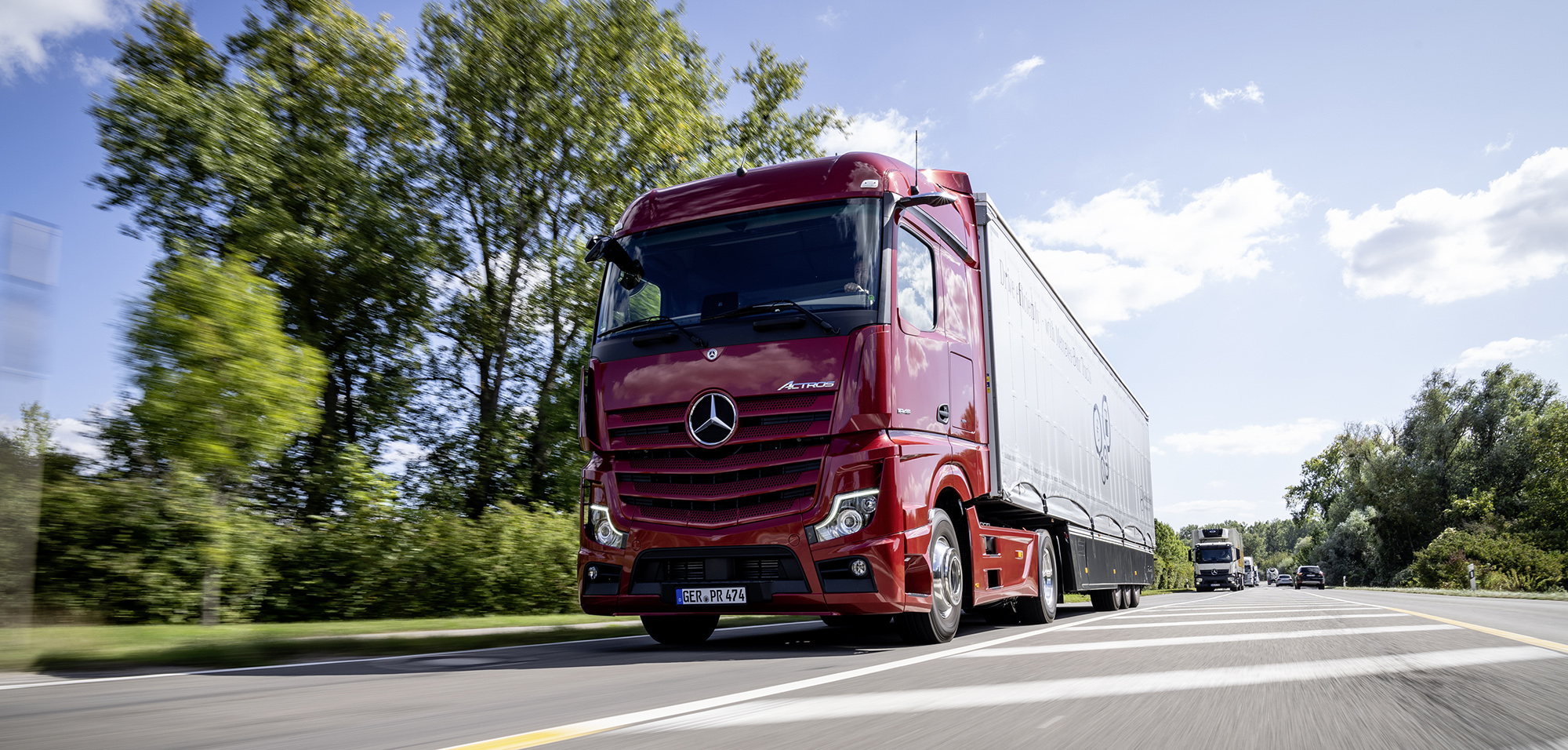
Mercedes Benz Trucks
Successfully exploiting eHPV potential with ProKon
28.11.2017
As many as 470 trucks leave the Mercedes-Benz factory in Wörth operated by Daimler AG every day. As in the cars division, the managers face the challenge of shortening development times and reducing manufacturing costs when a new product is launched. As the production department causes most of the manufacturing costs (machining parts and assembly work), it makes sense to start with cost saving or cost prevention measures even in the early phase of the product creation process – i.e. in the product development or design phase. The production planners at Wörth observed this best practice in the car division. MTM’s ProKon process is already the standard for assessing design solutions with regard to their effects on productivity there.
The aim of the pilot project with ProKon was to demonstrate any product potential for reducing the eHPV manufacturing time caused by its design (engineering hours per vehicle) taking the example of the “front panel”. More than 50% of the production time is defined by the design,” says Michael Müller, Production Planning – Assembly Strategy & Production Oriented Design at the factory in Wörth. “As a result, we’ve been looking for a method, which takes this into account and identifies adjusting levers in the product design. This also means communicating the requirements in the assembly processes to the developers and designers. We’ve been working on cost reduction measures for this product and in the process used for the current truck series for more than three years,” says Müller.
A team consisting of colleagues from the series preparation, assembly and production departments was formed for the ProKon pilot project – “but the employees in production provide the greatest input,” project manager Müller emphasizes. External support was provided by Deutsche MTM-Gesellschaft mbH, “for expert knowledge in work management and experience in the transfer of knowledge in the automotive sector were necessary,” Müller adds. But there was another reason for cooperating with MTM: The success of a project often fails because of a lack of proper analysis and documentation of the data. “I need dependable figures,” Müller adds, “and MTM provides them.” MTM is mostly used to determine standard times at the German Daimler factories.
A typical reference vehicle was chosen in advance and the distribution of the assembly times to the individual product departments was analyzed. The front panel was selected for the ProKon pilot project, as it is a structural component that involves a lot of assembly work with a clearly defined scope, distinct interfaces and therefore clearly defined responsibilities in the development phase. The front panel was initially assessed using ProKon in terms of its function, design and the work needed to assemble it. The next stage in the project involved working out the EHPV product potential, i.e. the development of design alternatives using ProKon and MTM expert knowledge. The target analysis led to EHPV potential of 36%. “Even if we’re only able to save one or two minutes in production time for each structural component, that all adds up in a year, given the number of trucks that we produce,” says Müller, projecting the figures forward.
Both the ProKon current analyses and the design alternatives in the form of the ProKon target analyses are documented using the MTM TiCon software. This means that all the data gathered in conjunction with the pilot project is structured and can be made available in a comprehensible form at any time.
Overall, more than 20 measures with design changes were described on so-called fact sheets and were passed on for assessment by the responsible developer teams, which consist of people from a wide range of departments. A decision on whether to introduce them will be made there, taking into account economic issues. The ideas are currently being assessed. Michael Müller is very happy with the pilot scheme. “The detailed analysis in terms of production times and the relevant documentation on fact sheets creates transparency for us, as we check and introduce the measures. The next step will once again involve the ProKon method to look for suitable EHPV potential when laying cables.”
Picture Copyright:
© Daimler AG