REFERENCES
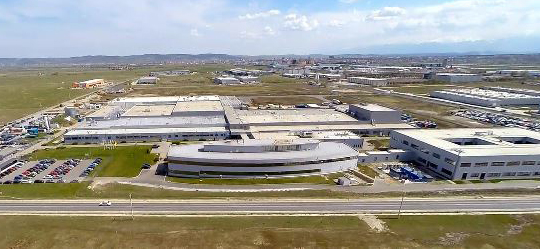
Continental AG
Supply Chain Managers Examine Productivity Potential
26.02.2019
Logistics Workshops at the Romanian Business Location
The international automobile supplier, Continental AG, which has its headquarters in Hanover, Germany, is planning to benefit from using MTM at its production site in Sibiu, Romania too. The corporation is initially focusing on logistics processes and particularly the issues of determining standard times, reducing throughput times and assessing human resources. The challenge involves having the materials available at the right place and at the right time – in a simple, speedy and flexible manner. The solution here is the internationally recognized MTM standard method.
Continental Automotive Systems SRL in Sibiu held several logistics workshops last year. The suggestion came from Continental in Germany, where the MTM standard method is already being used with great success. Management is interested in working with unified standards at all the production sites. Those attending the workshops – primarily supply chain managers – learned about the benefits of using MTM by studying real processes.
Potential savings of up to 13,000 hours per department and year
The participants paid particular attention to incoming goods and especially the unloading area, for example. Analysis and assessment with MTM logistics data as well as MTM-UAS, the process building block system that is most frequently used around the world, revealed savings potential of 3,000 hours per year here. Another department, where those attending the workshops were able to locate enormous potential, was the unpacking zone. As cardboard boxes are not allowed to be processed on the production line, parts and accessories are unpacked and repacked in special rooms. The savings potential uncovered by MTM amounts to approx. 8,000 hours per year here.
Those attending the workshops also gained experience in using MTM by picking and storing coils at the high shelf warehouse. The supply chain managers were more than surprised by the results: MTM unearthed savings potential of 13,000 hours per annum. The participants also grappled with alternative picking procedures like pick-by-light as well as different types of packaging. MTM was able to exactly quantify the productivity potential here too.
Monetary benefits of using MTM visible immediately
“It was particularly important for us to create transparency about the processes in the departments that we examined,” says Claudiu Dima, Head of Supply Chain Management at Continental Automotive Systems SRL, underlining his point. Another benefit of using MTM was that we were able to directly identify the first cases of waste in the logistics processes and quantify relevant improvement potential. “That’s what I call ‘productivity immediately’,” Dima continues. The corporation is set to gradually introduce the lists of measures prepared from the results of the workshops during the next few months. The enterprise is also due to examine and analyze other processes with MTM and then optimize them.
Picture Copyright
© Continental AG